How Volkswagen Overcame Challenges in US EV Battery Production
Source: Battery Technology Online
Volkswagen overcame significant infrastructure challenges in scaling EV battery production in the US, with Charles Abend highlighting global expertise, local supply chains, and innovative partnerships.
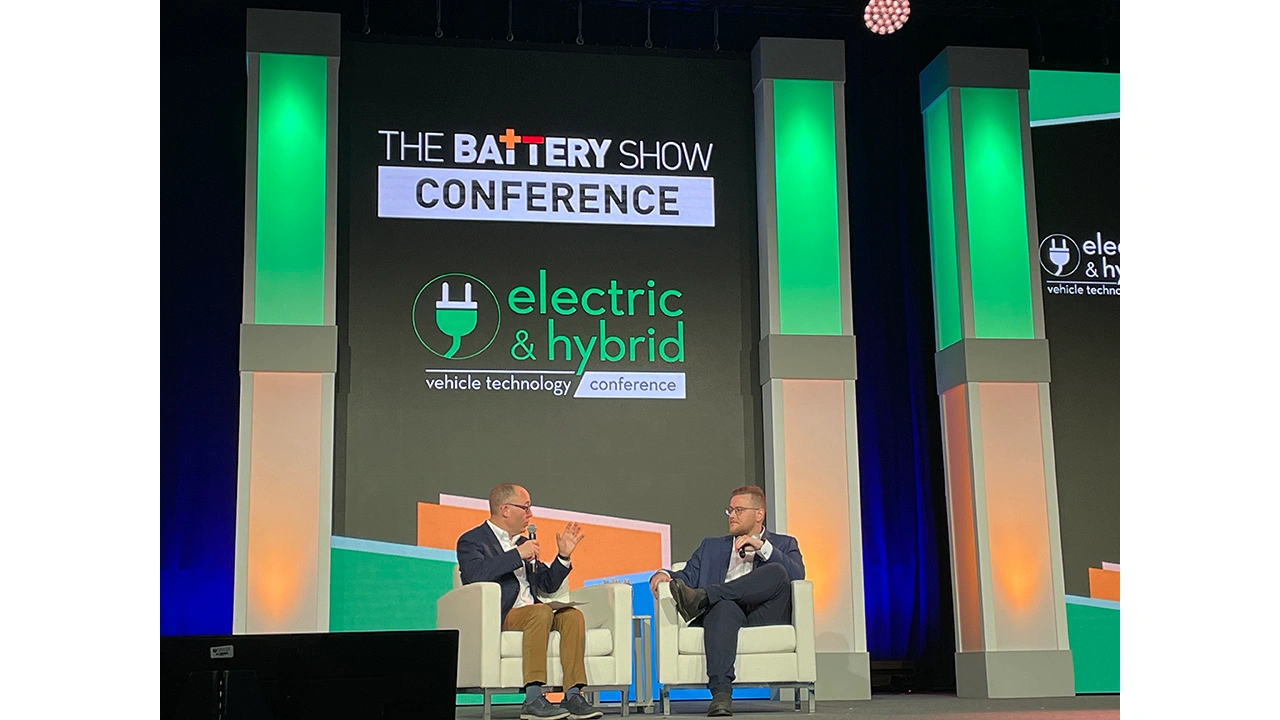
From left to right: Adam Halsband, Managing Director at Forward Engineering North America LLC and Charles Abend, High Voltage Validation at Volkswagen Group of America.Courtesy of Maria Guerra.
As electric vehicle (EV) adoption accelerates, original equipment manufacturers (OEMs) face significant hurdles in building the necessary infrastructure to support the production and development of EV battery packs. At The Battery Show North America, Charlie Abend, a High-Voltage Validation Manager at Volkswagen Group America—an integral part of creating Volkswagen’s Battery Engineering Lab (BEL)—recently highlighted Volkswagen’s unique challenges in scaling up EV battery production in the US. From creating local supply chains to building robust testing facilities, Volkswagen has had to make substantial investments and leverage global collaboration to meet the growing demand for EVs in the US.
Building US infrastructure from scratch
Volkswagen’s venture into EV battery production in the US prior to 2017 was limited. According to Abend, the company needed to build its EV battery production capabilities from the ground up. “I think we started making our first batteries in 2021, about January. This was massive. I think we’ve put $800 million […] since we started all these operations.” Abend said. This process required a significant financial investment to establish the US’s manufacturing, engineering, quality control, logistics, and testing teams. Unlike Europe and China, where Volkswagen had well-established EV battery production facilities, the US started with minimal infrastructure, which presented a massive challenge.
In addition to building the physical infrastructure, Volkswagen also needed to develop new processes and systems to manage the complexities of EV battery production. As Abend pointed out, the task of building an EV battery ecosystem was far more intricate than simply transferring existing capabilities from Europe to North America. The US market had unique demands, and the company needed to adapt accordingly.
Abend highlighted, “We had to start our engineering teams. We started production teams, quality, and logistics. Everyone had to learn requirements to handle better development batteries in the US.”
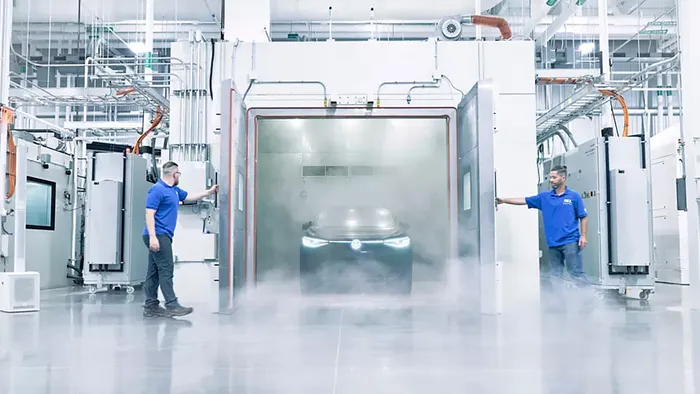
Charles Abend and Jeff Drumm with Volkswagen ID.4 test chamber at Volkswagen’s Battery Engineering Lab (BEL). Courtesy of Volkswagen .
Localizing the supply chain
One of the critical obstacles Volkswagen faced was localizing its supply chain to meet the Inflation Reduction Act (IRA) requirements, which incentivized EV production with US-sourced materials. For a global company like Volkswagen, which historically relied on international suppliers, transitioning to a localized supply chain was no easy task.
Abend noted that Volkswagen needed to work with local suppliers to adapt designs and ensure the necessary components were available in the US to meet IRA compliance, which may require reinterpreting existing designs to accommodate the local form factors. “We also need to make sure we’re using local suppliers, …because of the IRA compliance, which is a great move to the industry,” Abend said. This localization was essential not only for compliance with US regulations but also for logistical efficiency. As the demand for EVs grows, OEMs need to ensure that their supply chains are resilient, agile, and capable of delivering components quickly. Localizing the supply chain helps reduce lead times and strengthens relationships with suppliers, which is crucial for the smooth functioning of production lines.
Scaling the engineering talent pool
One of Volkswagen’s more unexpected challenges was the US shortage of specialized battery expertise. With a limited talent pool available domestically, Volkswagen needed to grow its engineering teams. Abend explained that the company’s goal is to increase its team size by 25%, focusing on hiring individuals with a “learning mindset” who could quickly adapt to the intricacies of EV battery production.
Instead of seeking only those with specific experience in battery technology, Volkswagen focused on hiring engineers in the US who could be trained in-house, leveraging the expertise of global teams to provide the necessary training and knowledge transfer.
“We now have solid teams. We’ve not had a lot of turnover. Now, we have a slightly different mindset when trying to find our talent. So, I’m not so much looking for the battery experts anymore. We can teach them the batteries. That’s no problem. What I am looking for is a mindset to learn. That’s the most important thing for us,” Abend concluded.
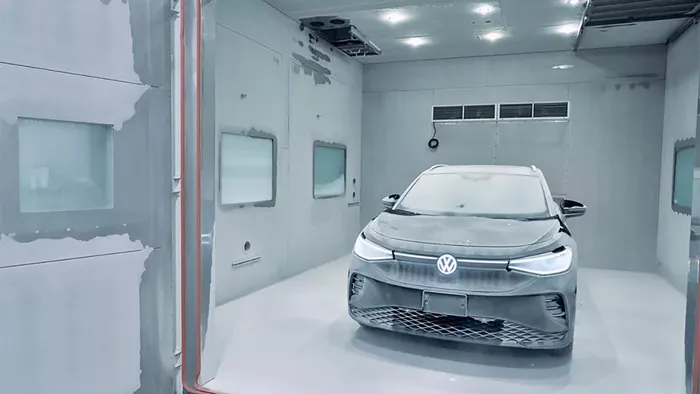
Volkswagen ID.4 EV tested at BEL. Courtersy of Volkswagen
Leveraging global collaboration
Volkswagen’s success in North America has been heavily dependent on close collaboration with its global teams, particularly those in Germany and China. Abend emphasized the importance of sharing knowledge and lessons learned from other regions. The early stages of building up the company’s capabilities in the US required significant knowledge transfer from experts in Germany, with Volkswagen sending personnel to Germany for training and embedding German experts in the US teams.
This global coordination has been essential in ensuring that Volkswagen’s North American operations are aligned with the company’s global standards and best practices. By leveraging the expertise of its global teams, Volkswagen has been able to fast-track its North American EV initiatives.
Strategic partnerships and innovation
Volkswagen has also formed key partnerships with research institutions such as Oak Ridge National Laboratory and local universities. “We started working with local universities like University of Tennessee at Chattanooga, Tennessee Tech….We’ve also started to work with other research institutes. Oak Ridge National Labs, which is an hour and a half north of us, and we are working with them right now in researching wireless charging.”
These collaborations have allowed Volkswagen to stay at the forefront of innovation, particularly in wireless charging and battery testing areas. By working with leading research bodies, Volkswagen can accelerate the development of cutting-edge technologies that enhance the efficiency and performance of its EV battery systems.
Volkswagen’s journey in building up its EV production capabilities in the US has been a complex and multi-faceted process. Through global collaboration, strategic partnerships, and a commitment to innovation, Volkswagen has positioned itself as one of the leaders in the North American EV market, paving the way for a more sustainable automotive future.